Wenn es darum geht, unterschiedliche Materialien wie Stahl oder Aluminium zu schneiden, gibt es eine Reihe von möglichen Verfahren, die angewendet werden können. Neben den herkömmlichen Verfahren mit einer Kreissäge, einer Stichsäge oder einem Winkelschleifer kommen dabei immer öfter innovative Schneidverfahren zum Einsatz, mit denen die Arbeiten wesentlich einfacher und präziser durchgeführt werden können.
Schneiden mit dem Laser
Zu den interessantesten Innovationen bei den Schneidverfahren zählt mit Sicherheit die Lasertechnik. Mit diesem Verfahren können sehr viele Werkstoffe berührungslos bearbeitet werden. Der Laser schneidet auf den Mikrometer exakt Materialien wie Kunststoff, Gestein, Papier oder Metall. Bei dem Verfahren wird ein gebündelter Laserstrahl wie bei einem Brennglas verstärkt und dann auf eine sehr kleine Fläche des zu schneidenden Werkstückes gerichtet. Das führt zu einer besonders hohen Präzision.
Zu den Vorteilen dieser Technik zählen vor allem die hohen Schnittgeschwindigkeiten, die große Genauigkeit und damit verbunden die gute Materialausnutzung. Dafür ist der Einsatz der Technik mit hohen Investitionskosten verbunden und es können auch nur begrenzte Materialstärken bearbeitet werden.
Schneiden mit dem Wasserstrahl
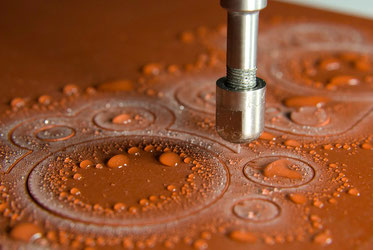
Im ersten Moment klingt es kaum vorstellbar, dass man mit Wasser Stahl schneiden kann. Doch mit dieser Schneidetechnik kann vom Saphir bis zum Schaumstoff nahezu jedes Material präzise zerschnitten werden. Der Druck macht es möglich: Beim Wasserverfahren wird mit einem Strahldruck von teilweise über 6.000 bar gearbeitet. Durch die Beimengung von Sand können mit dieser Technik auch sehr dicke Materialstärken von beispielsweise bis zu 300 Millimeter beim Material Edelstahl zerschnitten werden.
Die Vorteile der Technik liegen in ihrer hohen Wirtschaftlichkeit und der hohen Präzision. Darüber hinaus ist das Verfahren äußerst umweltschonend und sicher für den Anwender. Im Gegensatz zur Bearbeitung mit dem Laserstrahl werden dabei thermische Einflüsse unterbunden, die dazu führen können, dass sich das Material beim Schneiden verzieht.
Zu den wenigen Nachteilen der Technik zählt die geringe Schnittgeschwindigkeit und eine erhöhte Korrosionsgefahr des bearbeiteten Materials.
Plasmaschneiden
Auch bei der Technik des Plasmaschneidens konnten in den letzten Jahren deutliche Fortschritte erzielt werden. Dabei wird der Plasmastrahl auf eine Temperatur von bis zu 30.000 Grad Celsius erhitzt. Wenn der Strahl dann auf das zu bearbeitende Material trifft, wird die Wärme abgegeben und durch die Hitze aus der Schnittfuge geblasen. Je nachdem, wie sauber die Schnittfuge sein muss, kommen dabei unterschiedliche Gase zum Einsatz. In den meisten Fällen handelt es sich um Druckluft, es werden aber auch unterschiedliche Schutzgasgemische angewandt.
Vorteilhaft beim Plasmaschneiden ist vor allem die hohe Qualität in mittleren Materialstärken von 15 bis 40 Millimeter. Grundsätzlich können mit der Technik alle existierenden Materialien bis zu einer Stärke von etwa 200 Millimeter geschnitten werden. Doch Plasmaschneiden macht viel Lärm, was einen entsprechenden Hörschutz bei den Mitarbeitern erforderlich macht und verursacht dabei recht hohe Betriebskosten. Im Unterschied zur Wasserstrahl-Technik ist in den meisten Fällen auch noch eine entsprechende Nachbearbeitung des Werkstücks erforderlich.
Fazit: Die universell beste Technik gibt es nicht!
Die Schneidetechniken stehen nicht in Konkurrenz zueinander. Daher lässt sich auch nicht beantworten, welche Schneidetechnik denn nun die beste von allen ist. Im Gegensatz zu den herkömmlichen Schneidemethoden bieten jedoch alle den Vorteil, dass sie wesentlich präziser sind. Je nach Anwendungsfall können und sollen die Vorteile der unterschiedlichen Verfahren gezielt eingesetzt werden.